What are digital twins
Digital twins promise to deliver operational efficiency and new product, service, and business opportunities to the industrial sector. It is often linked with industry 4.0 and IOT with real-time data and analytics about your assets, but it is much more than that.
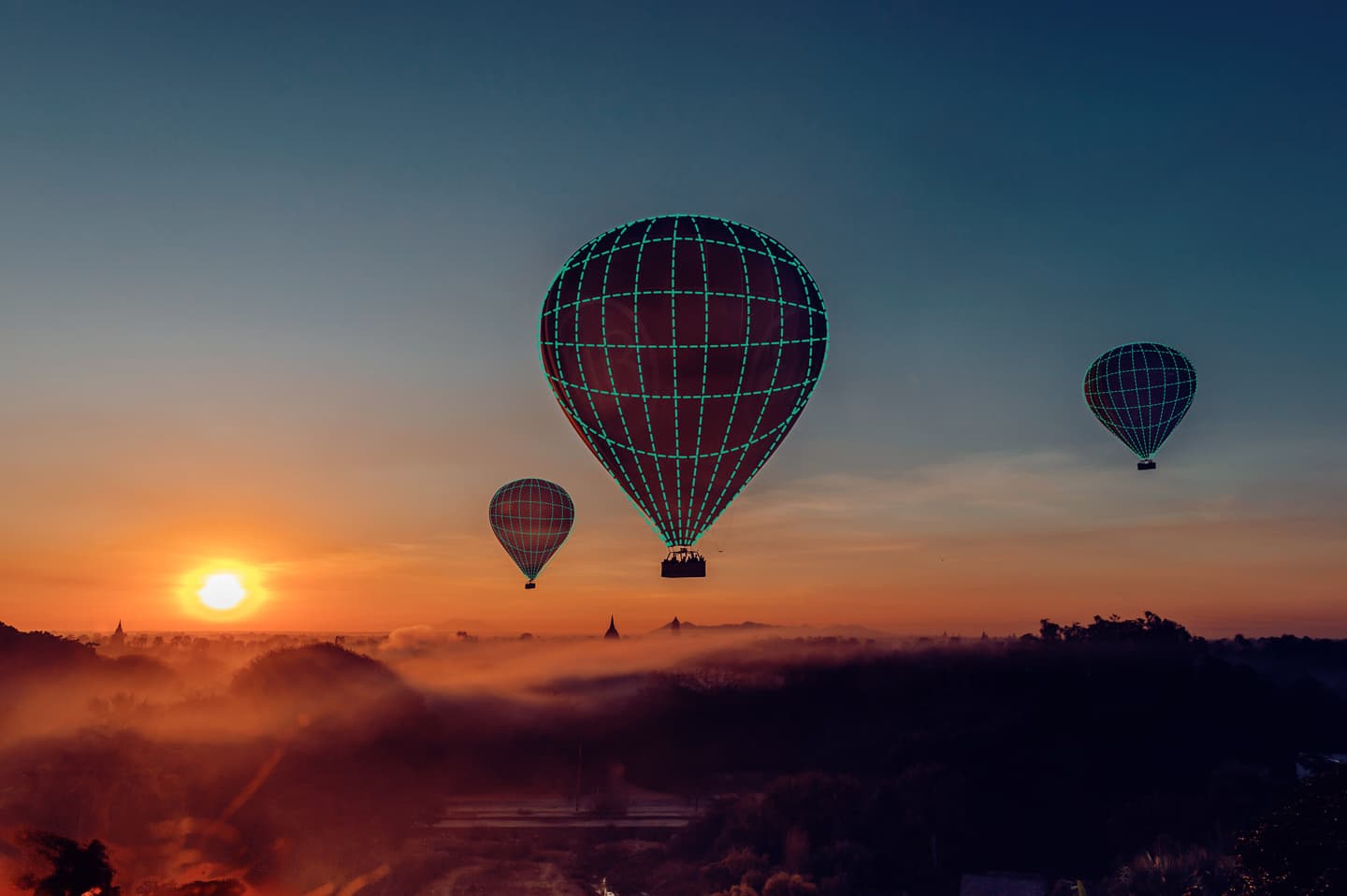
A digital twin is described as a digital representation of a physical product or system that can be utilized to analyse, simulate and control an asset throughout its lifecycle: from design to manufacturing, maintenance and decommissioning. It is a living data storage enriched during its lifecycle.
For a manufacturing company, a digital twin could mean a digital factory that enables predictive maintenance. For a construction company, it is a digital building that could be used to create an XR (extended reality) solution to “see” inside the walls when fixing the plumbing. For a smart city, a digital city that provides information to support urban planning and decision making by simulating an outcome that a new metro line has to the city's traffic, residential areas and services. For an automotive company, it is a digital representation of a car that could be used to offer value-added services to the end customer.
While a construction company working with AR goggles still might seem a bit far fetched, digital twins are entering mainstream use and have been in use for a while now.
More than a technological change
A digital twin is more of a new approach to data management than a single technology. It is about breaking organizational barriers and data silos by building cloud data infrastructure with modern microservices and APIs, which enables companies to share, query, analyse & merge information between different data sources. I believe this sharing, querying, analyzing & merging information cross-company is a prerequisite for value and benefits to be gained from digital twins and for industrial business transformation in general. It is an enabler for operational efficiency and new products, services and business models.
What the C-level needs to understand is that this paradigm shift in data management is not just a technological change. In the center of the shift are the people that define how industrial companies operate and how data is gathered and utilized. Although some parts of the data gathering and processing can be automated, for example with IoT sensors, a big part of it will still be a manual process performed by the workforce. Executive leadership needs to understand that employees need to be educated, work processes streamlined and user-friendly tools built to ensure the data integrity and quality of a digital twin.
The time to start is now
So when we talk about digital twins, we are actually talking about modern data management principles that enable industrial companies to improve operational efficiency and innovate new products, services, and business models on top of their data. Some technologies related to digital twins—such as XR—might still take time to mature, but it doesn’t mean that your organization can’t start reaping some of the benefits of digital twin “technology and data management principles” today.
Actually, your company probably has already started taking steps towards a digital twin by:
- Defining use cases for data to improve operations, and create new products, services, and business models
- Building cloud data infrastructure with modern microservices and APIs
- Transforming organizational culture and streamlining processes with agile and lean methodologies
- Developing user-friendly digital services for data gathering and analysis
And if you are not yet doing this, you should start now!
For more information about what we see in the future for the industrial sector, please download our point-of-view The Decade of Industrial Business Transformation.
- Oskari LiukkonenHead of Business, Enterprise Applications