A strategic response to labor shortage in the energy sector: Digitalizing processes and empowering data-driven decisions
As the energy sector shifts to renewable sources, it faces labor shortages and complex data needs. This blog explores digitalizing processes to address these challenges. Through a case study of an automotive OEM, we show how lean digital approaches can quickly enhance efficiency and transparency. Discover how customized solutions can transform workflows and improve efficiency in the energy sector.
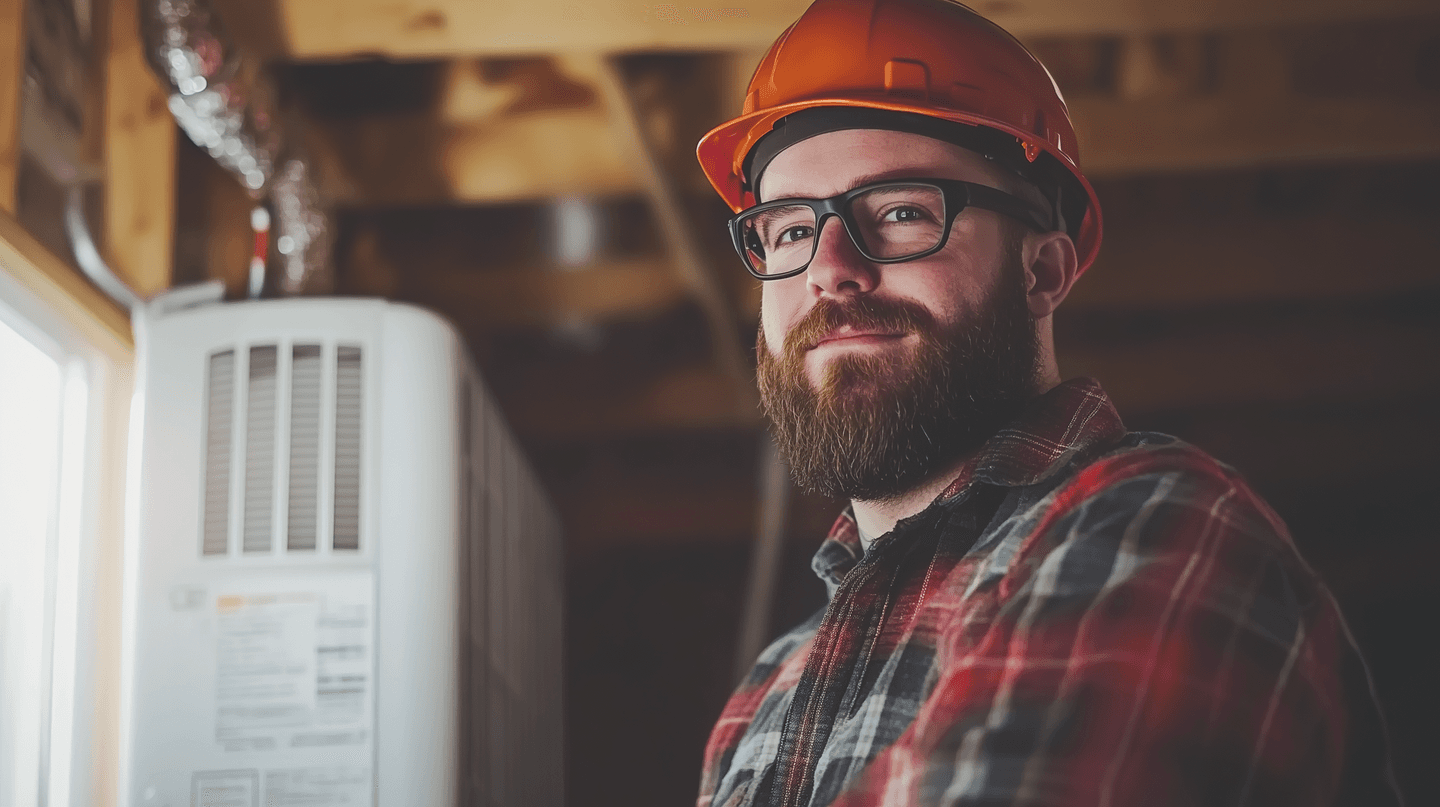
The emerging challenges in the Energy sector
The energy sector is transitioning from fossil fuels to renewable energy sources. This shift brings with it an increasing complexity of data and information. In a decentralized grid, not only assets need real-time automatic monitoring and control, but also the workflows for new energy hardware installation and maintenance are changing.
This demands robust digital systems. However, many energy clients are only beginning this transition, often still working with their organically grown legacy systems.
Coupled with an imminent labor shortage in operational roles, such as installers, mechanics, technicians, and customer support, energy companies are grappling with significant challenges in their ecosystem:
- The demanding and cumbersome nature of operational work presents challenges in filling these positions.
- Operative personnel is frustrated by an increasing number of apps not meeting their specific daily needs
- Inefficient processes lead to lower revenues due to manual paperwork and the overhead caused by the lack of system integration
- Lack of data available and its quality lead to missed business opportunities
Similar challenges can be seen at the intersection of energy and mobility – for instance in the aftermarket sector of automotive OEMs. A shortage of skilled workers is hindering the market move towards EV, paper-based processes are leading to inefficiency and a lack of transparency, and the tendency of most owners to pursue a maintenance strategy of run-to-failure leads to sudden damages which complicates planning. OEMs are also operating in a complex ERP landscape with many legacy systems that can’t be integrated without a lot of effort.
To navigate these challenges, digitalising processes and workflows is a strategic and highly rewarding investment.
Digitalising processes and workflows – A case study: How to mitigate labor shortage and information complexity
Consider the case of an automotive OEM we worked with. Their challenge was "How to adapt after-sales and aftermarket processes to cope with challenging conditions?"
With the newest generation of vehicles, it’s crucial that workshop employees have quick and direct access to vehicle data. Our research identified data transparency as key for efficient shop floor processes. This is what we set out to achieve with the digitalisation of their aftersales workshop processes.
We didn't aim to connect all legacy systems and data sources via APIs to create a digitalised “master process”. This would need massive upfront investment and take several years for the first results to appear.
Instead, we used a lean approach that enables us to create measurable outcomes within an extremely short time. We did this by following these three steps to achieve data transparency:
Create situational awareness: We combined data sources to get transparency of the service core process performance. We answered questions like: “What data is where?” and “Which workshop roles need which data and when?” For example, a workshop foreman has completely different needs than a mechanic working on a truck.
Change behavior and processes: The transparency gained allowed us to create new processes for improving the employee experience. For instance, we introduced a digital-assisted knowledge management, helping technicians access information at the right time – while empowering them to suggest new tasks they can perform.
Support more processes with data: To improve the system, we repeatedly fed the process with more data and created learning loops. Workshop data was used as input for further development activities within the OEM's R&D department. AI was used to analyze the dataset for patterns, spotting trends, and raising flags if needed.
This approach improved the throughput of the workshop core process, leading to a significantly higher workshop utilization rate. It also increased process transparency, enabling quicker feedback to vehicle owners or fleet managers.
Digital workflows also enhance operations like energy asset installation and monitoring, and energy usage improvement. For example, installers currently manually calculate heat pump performance and document their work. Streamlining these tasks increases their capacity for more valuable work, like customer advising or craftsmanship.
The power of customized solutions: The Futurice approach
Off-the-shelf solutions often fall short in addressing the specific challenges within complex contexts and thus in the energy sector. Customized solutions that are tailored to your unique processes offer instant value.
That's where Futurice comes in. As experts in digital innovation, we design, develop, and implement customized solutions that integrate seamlessly with existing systems. We are the task force that engages in direct exchange with the operational staff and listens to their requirements.
We leverage advanced AI technologies to unlock efficiency and overcome labor shortages. By customizing these solutions to your unique requirements and those of your staff on the ground, we can help your company adapt to the changing demands of the energy sector.
In conclusion, labor shortage in the energy sector is a significant challenge, but it also presents an opportunity for transformative change. Futurice is ready to partner with you in this transformation, ensuring your company's future success in the energy sector.
Does this resonate with you? Feel free to directly contact us. We are happy to exchange with you.
Your five key points to take away:
- Transition to renewable energy sources with high demands regarding digitalisation and efficient workflows meet an imminent labor shortage on the ground
- Operational roles become increasingly unattractive and processes lack efficiency and data quality
3 steps to start digitalising processes:
- Create situational awareness – know the daily workflows and their requirements
- Change behavior and processes – improve with insights through the transparency gained
- Support with data – enhance processes with data and uncover new opportunities
Off-the-shelf solutions are tempting but fall short compared to customized solutions which integrate seamlessly, create instant value and nail requirements and needs on point
- Benedikt BandtlowSenior Service & UX Designer